Maintaining multiple business software systems can be a costly endeavor, and could be holding you back from reaching your full potential. The real costs of running multiple siloed systems include more opportunities for data entry errors, an inability to catch errors by cross-verifying, lost efficiency, and difficulty locating parts at any point in your product stream. Moreover, the costs of purchasing and maintaining each of these separate systems multiply as you add more complexity. Streamlining your system down to a comprehensive enterprise resource planning solution can drastically improve the customer and user experience, while also eliminating waste at every step.
Missing Data
One of the biggest problems with multiple software programs working independently is the opportunity for data entry errors. Each time the information has to be entered into a new program such as your business POS software, you increase your chance for an error to occur by 3-5%. With a single cohesive ERP system, all of your automotive parts must only be entered once, and then the system will automatically reference your previous entries to verify for accuracy. Errors can be caught at the point of data entry, rather than downstream once the order has been placed, or perhaps after delivery to the customer, which can cost hundreds or thousands of dollars to fix.
Inefficiency
Aside from the propensity for data errors, separate systems also cause a major slowdown in the communication of important details. Whether finding parts, placing orders or tracking shipments, employees are forced to enter multiple screens, switch between functions and constantly revisit work they've already done. This inability to pull data from existing entries is a huge inefficiency that could be costing you money over and over again. In addition, it can be excruciatingly frustrating for a customer who calls in with a simple question and must wait for your employees to flip through countless programs to get the information they need. This leads to higher customer churn and lower transaction values across the board. In other words, it could literally be keeping you from growing your business. The worst part is that you can't even see where the inefficiencies exist because they are so deeply embedded in all of your tasks.
ERP works to eliminate inefficiencies by cutting down the time it takes to find information and flagging any items that appear to be in error. This allows you to go straight to the heart of the problem and deal with it immediately. In addition, it provides customers with more tools to track their orders so you don't have to manually follow parts through each step of your warehousing process.
Reporting
Yet again, multiple software systems present a problem when it comes to getting clear and concise reports. You will find that you have financial data spread across each department's software, but that information is never brought together to give you a big picture view of your performance.
With ERP business management software, all of your data is brought under one umbrella where it can be used to obtain up-to-the-minute reports. Your dashboard allows you to track real-time performance numbers. In addition, the system will highlight areas where money is being lost so that they can be addressed promptly.
Any automotive company can revolutionize their process with the help of an ERP system. Even small and mid-sized manufacturers or assembly facilities can save money by eliminating waste in their software and maximizing efficiency. The first step is to assess how much you are currently spending on your system and the cost of errors within that system. Then you can easily see how much you would save by bringing all of your data under one system where it can be used more effectively for better customer retention and higher volume sales. Remember, you're not just losing money, you're also losing time at every turn. Now is your chance to put a stop to the waste and learn about our all-inclusive ERP solution.
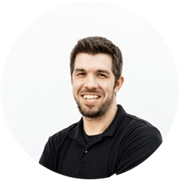
Brian Esh is a Sales Consultant at Koble who is passionate about following Jesus and helping small businesses grow. Brian has spent nearly a decade working with numerous business leaders to facilitate growth by putting software to work. When not working, Brian enjoys competitive sports and spending time with his wonderful wife and two children.